Have you noticed anything weird in your mobile home lately? Maybe you were walking through your kitchen, stepping out of the shower, pulling laundry out of the washer machine, or stepping over to the window to let some fresh air into the room. All of a sudden, you feel a little lower than you should be.
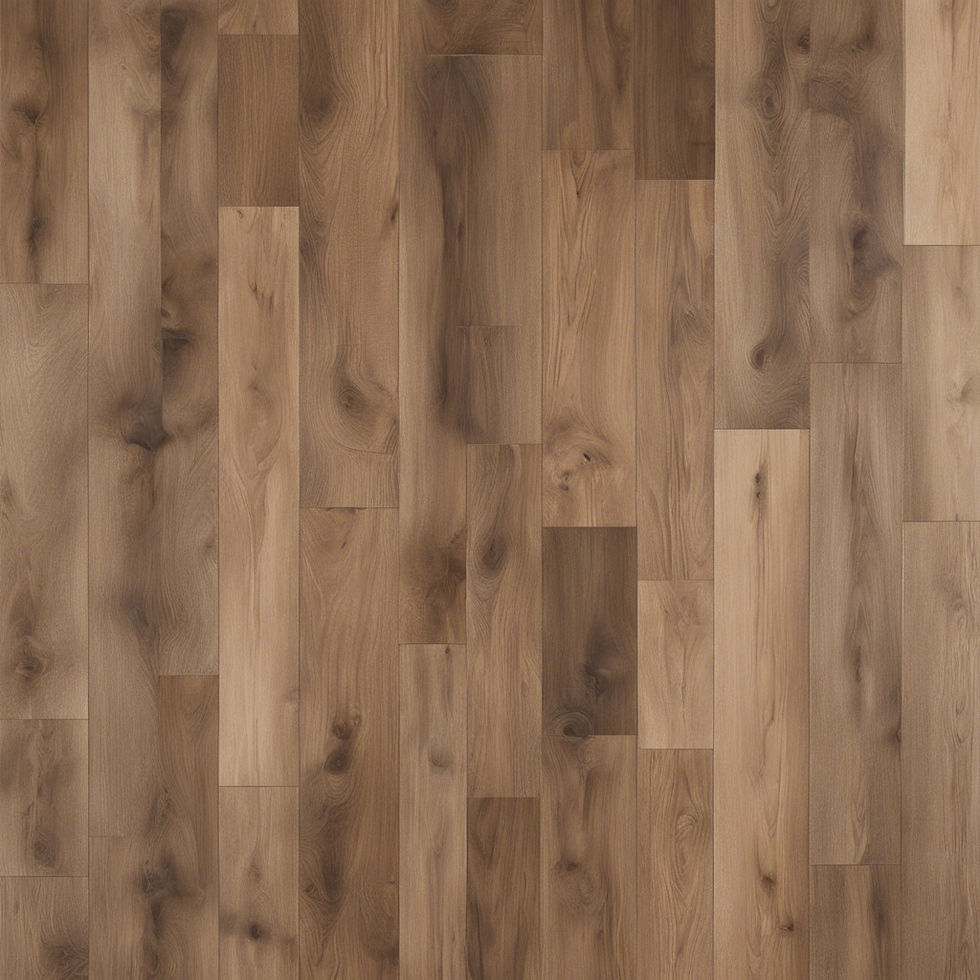
FLOORING TYPES
Soft spots on the floor can cause damage to other aspects of your mobile home. So it is important to find them sooner than later and take care of them. Before we cover how to replace the flooring in your mobile home, we should go over exactly how carefully you should watch for soft spots.
If you have an older mobile home, your sub-flooring most likely consists of particle board. Not only is particle board not the most durable material for flooring, but it is also extremely absorbent! Particle board works like a sponge; it sucks up water as soon as it touches it. The floor will get soggy and eventually rot. One too many steps turn a soft spot into a booby trap by letting your foot fall right through.
Newer mobile homes will have it a little better than older ones. Newer mobile homes will either use a better particle board or oriented strand board (OSB). Both of these materials used for flooring are much better in regards to water resistance. However, even homes with these newer flooring materials, the floors can still bow, soften, and warp.
Regardless of the date your mobile home was manufactured, if you find soft spots, the floors should be replaced before the joists and walls are also damaged.
HOW DOES THE FLOOR GET WET?
The most common way for water to get into contact with your floor is a leak. One possible source would be a leak from the roof that goes through the wall and into the floor. The leak in the roof could be caused by damaged shingles or water dams on your roof. Another source of a leak could water pipes that run through the flooring and into the walls.
If your leak is coming down from the roof into the floor, then you will need to repair that issue before you can solve your soggy floors. We wrote an article on roof maintenance that would be extremely helpful if that is your case!
WHERE SHOULD I LOOK, OR STEP, TO FIND SOFT SPOTS?
Soft spots tend to be found just by stepping on them and saying, “Oh? That’s not right!” However, some soft spots may not be in your usual walking path. Remember, just because you have not stepped on them, does not mean there are none in your home.
There are a few places you should check for soft spots regularly;– Check your bathroom floor regularly! There is a lot of water running through there (toilet, sink, bathtub, shower, water pipes, etc.)
– Occasionally move your washer machine and check the floor underneath. Sometimes the water line, or the machine itself, leaks and then seeps into the floor.
– Another pesky place for soft spots to form on your floor is underneath your windows.
– If you have potted plants in your mobile home, check underneath them occasionally for soft spots.
Checking around all of the places listed above will not only protect your home from greater physical damage, but it may also protect your family’s health. When water is absorbed into something, and it does not dry, what happens? Mold happens! Mold contributes to various illnesses, so the best option is to find any soft spots, fix the leak that caused it, and then replace the floor.
As an extra tip, if the floor in your bathroom has soft spots, then the water damage most likely has spread underneath the wall into the adjacent bedrooms.
REPLACING MOBILE HOME FLOORS
Now that you’ve identified the soft spots in your floors, it’s time to fix it. In seven easy steps, we’ll help you replace your floors and get your home back to normal. Here’s a How to guide to replace mobile home floors
WHAT WILL I NEED?
This DIY project will take some tools and materials, so it’s better to get those ready before you start. Check out the lists below.
Tools:
– Blade
– Circular Saw
– Face Masks
– Gloves
– Hammer
– Knife
– Level
– Prybar
– Scrapper
Materials:
– 2×4’s
– Galvanized Screws
– Liquid Nail Adhesive
– Plywood (3/4″ or 5/8″)
LET’S GET STARTED!
STEP 1: STRIP THE ROOM
Since you will be cutting into the floor in a later step, you will remove anything on top of your floors. If you have carpet in your bathroom, you will need the strips of carpet. Tile needs to be ripped up, and if you have vinyl, it will need to be cut around the perimeter of the bathroom and removed.
No only what is directly on top of the flooring, but you will also need to take out any trim that you have in the restroom.
STEP 2: CUTTING IT UP!
Next begins the cutting stage. I know, I know, this sounds like it will be the best thing ever, but it is better to be realistic, so you don’t lose steam during the project because of unmet expectations. Most people do not like the cutting stage because it is tedious due to the level of carefulness you must have.
First, depending on the thickness of your floor, most likely either 3/4″ or 5/8″, that is what you will want to set your circular saw. After adjusting the saw to the correct depth, you will then cut the perimeter around the bathrooms edge. Again, make sure the saw is adjusted to the right depth because you do not want to damage any of the joists below.
Second, after the first step of cutting, you now have a giant piece of floor sitting in your bathroom just ready to be removed … “Uh, how do I take out?” Good question! We’ll have to make that giant piece of flooring into small pieces of flooring … by cutting it!
Make sure that no wires or pipes are running between the joists first. If you are in the clear, then go ahead and make a cut between the joists where there is no electrical or water running between them. With the smaller pieces you made by sawing between the floor supports, you will be able to remove the pieces of flooring much easier.
ANOTHER REMINDER: Make sure that you check the saw blade (depth that the saw will cut) is accurately adjusted because you do not want to damage the joists or have any other accidents. The joists are your friends; they are what provide most of the support while you walk through the rooms in your mobile home.
Use a knife or Dremel to remove any of the subflooring underneath the walls. However, once you eliminate the subflooring under the wall, your wall will not have as much support, especially if the wall is not resting on a joist. If it is not resting on one, place an extra piece of wood or any makeshift spacer to keep your mobile home wall supported.
STEP 3: SCOPE IT OUT AND PROTECT FOR THE FUTURE
You should have bare floor before you, now that you’ve gotten rid of the soft spotted sub-flooring. Grab your gloves and face masks and start cleaning. Remove any of the insulation that was below the sub-flooring.
At this point, you can take a better look to see if you spot any more leaks. If you find any, track down the source and deal with it first. If you ignore the source of the water, then you will have the same problem even though you just replaced the floor!
Next, take your time to inspect the joists themselves. Look them over closely to assess if there is any water damage. If you do see any damage, you have three options:
– Add another 2×4 to damaged one to restore any strength lost due to damage. This one would be the easiest option.
– Replace the original 2×4 with a new one.
– Replace the original 2×4 with a new one and then add an extra 2×4. This option would be the strongest and longest lasting since it utilizes two brand new 2x4s.
STEP 4: INSULATE
After taking care of the joists, go ahead and put in some insulation. Use whatever is the best on the market for your budget, because high-quality insulation can save you on your utilities during the summer and winter seasons.
Where you have piping and wires, make sure that the insulation is underneath them and not on top. It is important that the heat in the home can reach them, especially those pipes when it comes winter time. No one likes burst pipes, or doing another floor replacement!
STEP 5: A NEW FLOOR FOR YOUR WEARY OL’ FEET
Let’s put some floor down! Or, at least the sub-floor. Above we talked about the different materials commonly used for mobile home floors, whatever you choose, make sure it is the same thickness as the last sub-floor, that way it will fit underneath the wall properly.
First, here is a little tip for before you lay down the new sub-floor. Attach new 2x4s around the perimeter of the room. The new 2×4 will create lip or shelf. You can use that shelf to have an easier time laying, gluing, and nailing down the new sub-floor.
Second, when installing your new sub-floor, you will want to lay the flooring in the same direction as it was originally before the replacement process began. This usually means that the new floor will be laid in the opposite direction of the joists. Make sure to that the plywood is cut to the correct size to fit the width of the room.
Third, where one piece of plywood meets another, a seam will be created. You will need to install another 2×4 between the joists so you can glue and nail the plywood, without the 2×4 there will be nothing to anchor the new sub-flooring to which can lead to the new floor shifting when you walk on it. If you miss this step, it will hurt you in the long run.
Fourth, regularly check the level of the floor. If you see that it is unlevel, you can always add or remove what you need to from the joists to make it level. No need to make it feel like you are trekking over the Himalayas when you walk from one side of the room to the other.
STEP 6: TUCK IN YOUR NEW FLOOR WITH SOME COVER
If your desire to express yourself has been restrained by having to follow the above directions closely so that you have a long lasting floor, then you can let the creativity flow at this point.
Floor covering options come in many types and styles. You can go with carpet, vinyl, tile, and some even do hardwood if your mobile home can handle the extra weight. We recommend either vinyl or tile for bathrooms since these two options do a better option with keeping water from getting into the new sub-flooring.
STEP 7: USE IT!
This is the easiest step of all! Now that you’ve successfully replaced your floor, it’s time to take a break. Enjoy your new floors. Take pictures of your handiwork. Walk on your latest creation. And when your friends marvel, you don’t have to tell them that replacing mobile home floors isn’t really that bad! Your secret’s safe with us.
PREPARING FOR YOUR MOBILE HOME FLOOR INSULATION
INSPECT YOUR MOBILE HOME FLOORING
First, inspect the underside of your mobile home to check for damages like holes or water buildup in the flooring. If you find any damages, repair them before you add insulation. Also, remove any existing insulation. If you find any holes, you can fill them with insulation stuffing or wood cutouts to seal them. For accumulated water, dry it up completely to prevent mold growth before you insulate your floor.
TAKE PRECAUTIONARY MEASURES
Make sure there is as much space as possible before installing insulation. Place insulators over any plumbing and wiring. Consider switching off the water and power supply to prevent any accidents.
Most manufactured homes come with fabric road barriers or fiberboards to protect the home’s undercarriage while transporting units. In order to install mobile home floor insulation, you’ll need to remove the fiberboard barrier. Don’t forget to reinstall it once you’ve put in the new insulation.
PURCHASE INSULATORS
You can buy any floor insulation as long as it has sufficient R-value. You will place the insulators at the floor joists on the underside of your mobile home starting from the front of the main beams towards the end.
INSTALLING YOUR MOBILE HOME FLOOR INSULATION
Before insulating your floor, lay a moisture barrier beneath your mobile home so that it can prevent the ground moisture from infiltrating the insulation. Besides that, it will be easier to lie on a barrier than on the plain ground. A suitable barrier would be a polyethylene plastic sheeting. Start insulating at the ends of the first and second joists with the paper backing turned down. Secure the backing by stapling the ends to a wood frame then attach wires to secure it even further. Continue with the same process until you finish with the rest of the insulators.
Be sure that the wiring, plumbing and duct tape runs below the bottom of the insulation so the insulation layer can be continuous. You can use insulation butts that have vapor barriers and install them with the barrier facing either up or down, depending on where you live and the kind of weather you experience. Make sure that the butts are cut to the right width so that they fit perfectly. Any gaps in the insulation could be passageways for cold airflow.
RECONNECT WIRES AND PLUMBING
Once you finish, you can reconnect the pipes and wires you had previously disconnected. Use silicone sealants to close plumbing lines and insulate the plumbing and ductwork with wrapping insulators as well. Cover the wrapping insulation with duct tape afterward.
COVER THE INSULATION
Next, cover the insulation with fabric or plastic fabric sheeting to reduce condensation. Regardless of the type of fabric, it is important because it will prevent cold drafts from seeping through your insulation.
REATTACH THE ROAD BARRIER
Finally, reattach the road barrier the same way you removed it. Make sure you secure it as best as possible and if damaged, replace it and install it. If you leave this step undone, you may end up with unwanted critters living under your home.
INSULATING THE CRAWLSPACE
Insulating your crawl space will save you from high energy costs and will increase the comfort of your home. The insulation of your crawl space will depend on whether it has proper ventilation or not. If your crawlspace is unventilated, you should seal and insulate the foundation wall. If you manage to avoid issues associated with ventilated crawlspaces, you will require less insulation and air sealing will be much less critical.
REDUCE ENERGY COSTS WITH A MOBILE HOME FLOOR INSULATION
These are just some of the steps you can take when installing mobile home floor insulation to enhance the comfort of your home and reduce energy costs. Mobile homes are more susceptible to losing heat
Comments